Navy Qualification Tests Passed & Approved
These innovative superalloy flight deck tie down fittings, also known as tiedowns, successfully passed the Navy's Qualification Tests as well as Corrosion and Fatigue tests. See the summary of the results below.
Corrosion Test Setup & Results
The objective of this corrosion test was to determine the seawater corrosion resistance of the two Inconel 718 parts (machined and DMLS fabricated) and if they differed in resistance and also evaluated was the galvanic compatibility of AISI 4130 steel plate welded to a part made of Inconel 718. Lastly, a sample of unprotected AISI 4130 steel rod was utilized to show the contrast between noncorrosive resistant material versus the high corrosive resistance of Inconel parts. The AISI 4130 steel plate, at the beginning of the test, to prevent its corrosion had two coats of primer paint applied followed by two coats of enamel paint applied. A few days later it was observed that some areas of the steel plate were corroding because of the severe corrosive environment and due to defects in the coating which did not cover all areas of the steel so several more coats of paint (primer and enamel) needed to be applied to the AISI 4130 steel. This was done to avoid contamination of the Inconel 718 samples. Any defects in the steel plate paint coating showed up promptly.
Setup:
Results:
​
The results of the Inconel 718 parts indicated that no corrosion ever was present. The Inconel parts after 3 months were bright, shiny, and there was no evidence at all of corrosion and were completely unreactive to the constant exposure to seawater in a very high humidity simulated marine environment. The Inconel 718 DMLS fabricated tiedown and the machined cylinder of Inconel 718 material were both completely unreactive to daily splashing of seawater and continuous partial immersion in seawater. There was no difference in the corrosion resistance of either Inconel 718 test sample which proves that a DMLS fabricated Inconel 718 part has equal seawater corrosion to a machined part made of Inconel 718. Both were completely impervious to seawater corrosion. As expected, the AISI 4130 control sample immediately began corroding within minutes of exposure to seawater and after 3 months was heavily corroded.
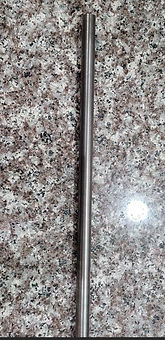
Figure 1. 4130 steel rod during Day 1 of the Corrosion test.

Figure 2. Inconel 718 tiedown welded in steel plate during Day 1 of the Corrosion test.

Figure 3. Corrosion Test results at the end of Day 92
Note that the 4130 steel rod (shown at bottom) was completely corroded, yet the Inconel 718 tiedown (left) and the machined Inconel 718 part (right) were completely impervious to corrosion at the end of the test.
Static Pull Test Results & Setup
​
Two qualification tests, called the Shop and Installation tests, were performed to provide proof that this new Inconel 718 tiedown was fit for service on an Arleigh Burke destroyer. Specifically, the Shop and Installation test for 4 bar tiedowns was followed as described on Navy reference drawing 1916300, Rev P, page 15. See the “Test Notes” of said drawing for the procedure utilized in these tests.
​
During the Shop test, the tie down was loaded to 25,000 lbs. asymmetrically with one hook and held for one minute. Then the same test was repeated with a hold for five minutes. Our Shop test was actually even more severe than called for on the Navy drawing.
The Navy drawing only specifies that an asymmetrical load of 25,000 pounds be applied and then immediately released to pass this test. Instead, we applied the load for one minute and released it and then applied it again and programmed the machine to hold the load for 5 minutes before releasing it. The very high strength hook snapped and broke after 4.5 minutes, dynamically releasing the load suddenly. So impressive is this design that no damage was done to the Inconel 718 tiedown.
​
The tiedown used symmetrical loading with two hooks (installation hooks) loaded to 32,000 lbf and it was held for one minute. The same test was done again but with a hold of three minutes.
​
Results: The Inconel 718 fabricated by the DMLS process and heat treated passed all tests proving it meets all Navy requirements for service as a tiedown on an Arleigh Burke destroyer.
Qualification Static Vertical Pull Tests (25,000-pound asymmetrical Test & 32,000-pound symmetrical Test) Results:
Shop Test Setup:
Installation Test Setup:
Click on the icon above for a link to the full ATS static pull testing report.
Fatigue Testing Results & Setup
Testing Setup & Background:
​​
Since this new Inconel 718 tiedown is completely impervious to seawater corrosion and can now last for the full 40-year service life of an Arleigh Burke destroyer it would be imprudent not to consider the expected fatigue life of this new tiedown. Since no data is available concerning the probable service load spectrum, engineering estimates had to be drawn upon to arrive at a reasonable load spectrum for this fatigue test. Knowing the purpose of and uses of these tiedowns on a destroyer it was decided that a million cycles at 5400 pounds would adequately prove that this Inconel tiedown would not fail in fatigue during service conditions.
​
​
​
​
For this fatigue test 1 million cycles of this load were applied which is a reasonable number of load cycles that one could expect this tiedown to experience in service over 40 years. After enduring and passing both cycles of the severe 32,000-pound symmetrical vertical pull static test and cycles of the 25,000-pound asymmetrical vertical pull static test with no damage or permanent deformation this same tiedown then endured 1 million cycles of an expected service load of 5400 pounds. If this DMLS part was inferior to a machined part we would have expected it to fail, but instead it passed all tests and is even now undamaged, and as good as new, and ready for millions and millions more service load cycles.
Results:
Click on the link above to open the full ATS fatigue report.